回收粉末的物性和含氧量会与原始粉末不同,其对打印的影响一直是人们研究的课题。英国国家结构完整性研究中心、考文垂大学、伦敦大学、莱斯特大学等单位的研究者发现,高含氧量的Ti6Al4v粉末可降低熔体飞溅、表面粗糙度缺陷。
Al | V | N | C | O | Fe | Ti |
6.37 | 3.98 | 0.010 | 0.015 | 0.120 | 0.182 | Bal. |
表1。本研究中使用的Ti6Al4V粉末的化学成分(wt.%)。
通过使用定制的粉末热处理炉人工氧化原始AGA粉末来制备高氧含量Ti6Al4V粉末。将原始粉末倒入炉内的不锈钢容器中,通过搅拌器使粉末翻滚/混合 以防止粉末在高温下烧结并确保均匀的粉末氧化。氩气保护状态下,将粉末加热至475 °C并保持5 h,然后进行炉内冷却。通过在整个热处理循环中吹扫Ar气体来控制容器中的氧气水平。使用插入熔炉容器中的热电偶来监测温度。使用70 μm孔振动筛过滤氧化的粉末,检查筛网后未发现烧结颗粒。考虑到先前研究中报告的回收Ti6Al4V粉末的最大氧含量为0.33 wt%,氧化实验的目的是将粉末氧含量增加到~0.40 wt%。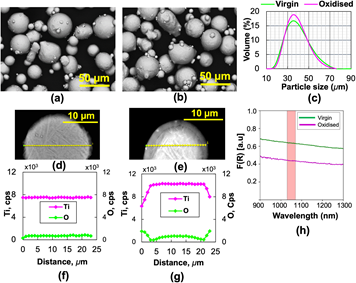
图1。(a)原始粉末(b)氧化粉末的SEM粉末形态BSE图像;(c)原始粉末和氧化粉末的PSD钟形曲线。(d)原始粉末颗粒和(e)氧化粉末颗粒的粉末横截面,分别具有相应的EDS线图(f)和(g);(h)Kubelka-Munk变换,F(R)漫反射。激光的波长(1030–1070 nm)由粉红色区域表示。
大多数原始的(图1a)和氧化的(图1b)粉末颗粒是球形的,带有一些常见于AGA粉末中的卫星和团聚体。与原始粉末相比,氧化粉末的PSD曲线略窄,这是在回收粉末中观察到的普遍现象(图1c)。原始粉末和氧化粉末的Dv(10)、Dv(50)和Dv(90)值分别为26、38和55 μm和27、38和54 μm。霍尔流量测量31 ± 0.04 s/50 g和30 ± 0.03 s/50 g。两种粉末都表现出连续流动,没有任何中断。氧化粉末流动行为的边际改善可归因于细颗粒的减少,如PSD钟形曲线左侧的轻微偏移所示(见图1c),或归因于热处理后湿度水平的可能降低。总体而言,粉末物理性能的变化只是微不足道的。原始粉末和氧化粉末的横截面分别如图1d和e所示。人工粉末氧化过程中的热处理温度保持在475 °C,远低于β转变温度(~990 °C),因此没有发生微观结构变化,并且两种粉末都由α′微观结构组成。SEM-EDS分析证实,氧化的粉末颗粒具有表面氧化物层,而原始粉末颗粒中不存在可见的氧化物层(图1f和g)。通过IGF-IR测量的氧化粉末氧含量显示0.40 wt%,即 > 比原始粉末高3倍(0.12 wt %)。由于粉末氧化是在低温下进行的,因此元素不太可能蒸发。因此,假设氧化粉末中剩余的化学元素,如铝和钒的含量与原始粉末相同。以F(R)为单位的UV-VIS-NIR反射率测量(图1h)表明,由于表面氧化物层的存在,氧化粉末的激光吸收率几乎是原始粉末的一半。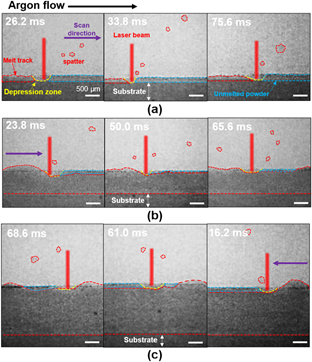
图2。原始粉末Ti6Al4V粉末L-PBF过程中, 第(a)1层、第(b)5层和第(c)10层激光与物质的相互作用和飞溅物。所有射线照片中的比例尺均为500 μm。红色虚线圆圈标记飞溅轮廓;熔化轨迹、未熔化粉末和凹陷区域的轮廓分别用红色、蓝色和黄色虚线标记。
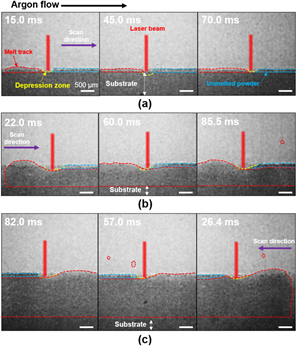
图3。氧化粉末Ti6Al4V粉末L-PBF过程中, 第(a)1层、第(b)5层和第(c)10层激光与物质的相互作用和飞溅物。
观察到团聚粉末飞溅的形成(Deq>60 μm)。粉末颗粒簇首先夹带在蒸汽羽流中,然后与激光束相互作用,形成熔融液滴,继续夹带在Ar流中。如果这些团聚的飞溅物落回熔池,或落在粉末床的未熔化部分时则可能产生缺陷,降低粉末的可回收性。大多数液滴飞溅物从熔池垂直喷射,不会干扰未熔化的粉末,随后沿着整个10层的Ar流动方向夹带构建。一些液滴飞溅还与激光物质区附近的松散颗粒碰撞,形成较大的飞溅,类似于参考文献中所述。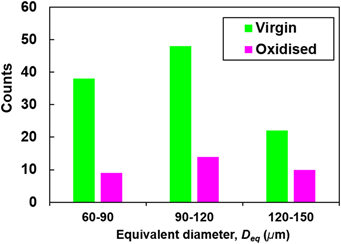
图4。前5层的原始和氧化条件下的L-PBF期间量化的液滴飞溅数量。
由于成像装置的大像素尺寸和高能X射线,Deq<60μm<>的小飞溅对X射线基本透明。飞溅分析中不包括Deq<60<>μm的粉末飞溅。为了避免结果中的差异,将重点放在熔池中出现的现象上,只分析Deq≥60 μm时的液滴飞溅。图4显示了使用原始粉末和氧化粉末在L-PBF构建的前5层中产生的液滴飞溅总数及其相应的Deq值。很明显,在前5层中,原始粉末产生的液滴飞溅是氧化条件的2到4倍。液滴飞溅的最大等效直径范围与粉末床颗粒的Dv(50)(∼38 μm)相比几乎高出四倍(120–150 μm)。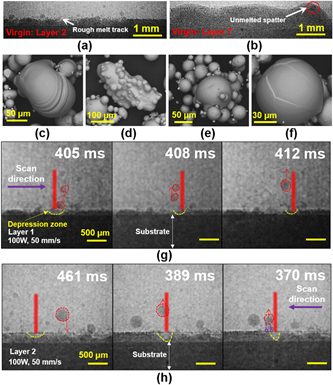
图5。(a)使用100 W激光功率和50 mm/ s扫描速度显示飞溅引起的表面粗糙度和飞溅;(b)使用150 W激光功率和50 mm/ s扫描速度显示飞溅(红色圆圈);(c)单个粉末颗粒上固化/烧结的飞溅;(d和e)具有不同长径比的颗粒的飞溅团块;(f)球形“超级球”飞溅。(g)一个液滴飞溅与另一个液滴飞溅合并;(h)粉末飞溅与一个液滴飞溅合并形成一个大飞溅。液滴飞溅用红色圆圈表示,粉末飞溅分别用紫色圆圈表示。
图5c显示了从激光-物质相互作用区喷出的液滴飞溅,随后落在粉末颗粒上,合并,然后凝固。图5d–e显示了飞溅引起的粉末团聚,这些团聚是由于喷射过程中液滴飞溅与周围颗粒的撞击或喷射的液滴飞溅落回粉末床的未熔合区域时产生的。图5f所示为“超级球”飞溅粒子,即液体飞溅物在其飞入大球形粒子(∼90 μm)。图5g示出了一个缓慢移动的小飞溅物与另一个飞溅物合并形成一个较大的液滴飞溅物。图5h显示了通过将液滴飞溅物(红色虚线圆圈)与粉末飞溅物(紫色圆圈)合并而形成的大飞溅物。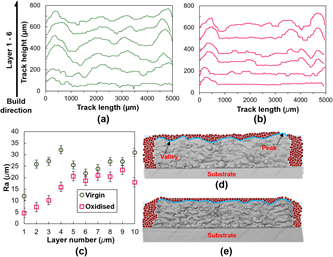
图6:。由(a)第1层至第6层原始粉末和(b)氧化粉末产生的L-PBF构建物的表面轮廓;(c)表面粗糙度Ra的平均和标准偏差,原始和氧化建筑中的测量值;(d)原始和(e)氧化条件下,层粗糙度对粉末铺展的影响,其中红色圆圈表示粉末颗粒,灰色对象为XCT渲染的薄壁结构。
在多层L-PBF构建过程中,先前凝固熔体轨迹的表面粗糙度Ra导致层厚度变化。Y轴上的每个分区对应于预设层厚度100 μm。沿轨迹长度,实际层高度与用户定义的层厚度相差很大。在原始条件下,层高度增加到最大260 μm,最小30 μm。在氧化条件下,层高度在30 μm和152 μm:与原始条件相比,实际层高度的变化相对较小。根据熔体轨道边界的X–Y坐标测量每个熔体轨道顶部表面的Ra值。图6c比较了原始粉末和氧化粉末生成的10层构建的Ra值。原始粉末形成的熔痕在所有构建层中的Ra均高于氧化构建。在这两种情况下,Ra在前几层急剧增加,然后随各层之间的边缘波动而稳定。由于使用X射线照片测量表面粗糙度既不是标准方法,也不是工业上通常采用的方法,因此根据ISO 4288测量原始和氧化建筑中最后一层(第10层)的表面粗糙度。原始粉末构建Ra值为14 μm,氧化粉末构建为3 μm。X射线片测量的相应Ra值为29 μm和13 μm,分别对应原始构建和氧化构建。两种技术测量的Ra值的差异可归因于其可分辨的空间分辨率和测量方法。两种结果都表明,原始粉末所产生的熔痕比氧化粉末所产生的熔痕更粗糙。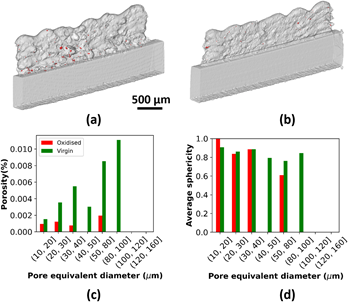
图7。在原始和氧化Ti6Al4V构建中使用XCT进行缺陷量化。3D渲染的XCT孔隙图像(红色)覆盖在(a)原始和(b)氧化薄壁结构(灰色)上。(c)孔隙率百分比及其(d)球形度与孔当量直径的函数关系。
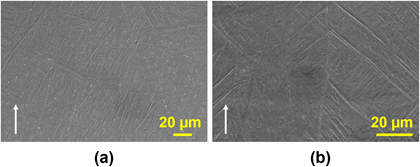
图8。(a)原始和(b)氧化生成微观结构的典型SEM图像。白色箭头指示构建方向。
图8显示了在构建方向上原始构建和氧化构建的微观结构。两种样品均呈现典型的L-PBF Ti6Al4V显微组织,主要由α′组成。正如预期的那样,原始粉末构建维氏显微硬度测量值从393 ± 10 HV,氧化粉末构建为461 ±8 HV。在L-PBF过程中,通常从激光-物质相互作用区观察到两种类型的熔体喷射,即粉末和液滴飞溅:(1)固体粉末飞溅(粉末-颗粒喷射)和(2)液滴飞溅(熔体喷射)。固体粉末飞溅发生在熔池周围区域,这是由于未熔合的粉末颗粒夹带到金属蒸汽射流中,而液滴飞溅则是由于对熔池表面施加了强大的反冲压力而从熔池表面喷出。图5a-f显示,无论有没有粉末团聚,飞溅物通常比原始粉末粗,即两倍于母粉末颗粒的尺寸。虽然当粉末回收时,在筛分过程中,大多数飞溅物可从后续构建物中过滤掉,但一些高长径比飞溅团聚体(图5d)可沿特定方向穿过筛子并最终进入粉末层,从而影响粉末流动和松装密度。当氧化飞溅颗粒落回粉末层时,也会出现导致粉末层化学不均匀性的颗粒。液滴飞溅量受输入能量密度、腔体压力和氧含量等工艺参数的影响。结果表明,在原始粉末产生的飞溅数量是氧化条件下的4倍。两种粉末的工艺条件或线性能量密度(LED)相同,因此,飞溅量的差异只能归因于Ti6Al4V粉末中氧含量的变化。在所研究的条件下,粉末表面的氧化层改变了导致飞溅减少的三种现象。首先,氧化后的Ti6Al4V粉末显示出铝在其表面富集,即优先形成氧化铝(高达60 纳米深度。由于氧化铝的存在,氧化后的Ti6Al4V粉末在1070纳米波长处的激光吸收较低。氧化粉末(图1f)的激光吸收减少(∼2倍)会减少粉末床上的LED输入,可能导致传导模式、熔体流动中的湍流、金属蒸发减少,从而减少熔体喷射。其次,熔体中氧化物作为表面活性元素的存在可以改变温度相关的表面张力梯度从负变为正,类似于文献]中报道的观察结果,从而逆转Marangoni对流从外向离心流到内向向心流。熔体流动方向的反转也会增加熔体深度,这在不同的工艺中已被广泛观察到,例如316L的电弧焊接、不锈钢的激光焊接、Ti6242的直接能量沉积(DED)和Inv36粉末的L-PBF。在这些研究中,一定量的氧作为氧化物在熔池表面保持不溶性,从而改变表面张力梯度,从而改变Marangoni对流。相反,氧在钛熔体中的溶解度很高。此外,TiO2的熔点和沸点(1843 °C和2972 °C)和Al2O3(2072 °C和2977 °C)高于Ti6Al4V(1668 °C),在L-PBF期间经历的温度可能超过这些温度,因此,表面氧化物可以作为氧物种解离到熔池中。当氧含量从0.009 wt%增加到0.04 wt%时,熔池粘度增加2倍以上。熔体池粘度的增加是减少熔体池中湍流的另一个因素。由于流动惯性大大减小,无法克服熔池表面张力,熔滴飞溅物无法从熔池表面逸出。这就解释了为什么氧化条件下的液滴飞溅数量比原始条件下的低4倍。再次,熔体轨迹的拓扑结构导致多层构建过程中粉末层厚度的不均匀性,如图6d和e所示。这意味着归一化LED(归一化LED = LED/层厚度)显著变化。例如:层厚度为230 μm,归一化的LED测量到13 J/mm2。而最高隆起区域的层厚度仅为30 μm,归一化的LED为100 J/mm2。在高归一化的LED上可以发生更多的金属蒸发,并且更有可能形成飞溅物。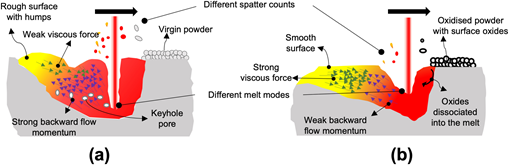
图9。(a)原始粉末和(b)氧化粉末在L-PBF过程中蒸汽抑制区、熔池和缺陷动态的示意图。
在焊接冶金中,熔体轨迹表面形成的起伏通常被称为“隆起”,由能量密度、表面张力、粘性力、毛细管力、反冲压力等几个因素控制。在参考文献中通过L-PBF工艺生产的Ti6Al4V原始熔体轨迹中也观察到了类似类型的波动。Nguyen等人确定驼峰引发的主要因素是能源后面熔体流动的强大向后动量。Gunenthiram等人报道称,隆起的发展是由熔体轨迹的大纵横比引起的,这会促进Plateau-Rayleigh不稳定性。唐等人进行的过程模拟表明,随着激光轨迹熔化的进行,第一个隆起的形成促进了更多隆起的发展,从而导致沿着熔体轨迹长度形成周期性隆起,如图6a和b。Leung等人假设快速流动的熔池上方快速流动的惰性气体在相反方向上会引起Kevin Helmholtz不稳定性,从而导致驼峰的形成。参考文献中开发的一个数学模型]还表明,随着粘性剪切力的增加,熔池的反向流动惯性显著降低,氧化粉末产生的熔池比原始粉末产生的有更高粘性,具有较低的熔体反向流动动量,减少了熔体轨迹的波动(图9)。以往研究通过调整工艺参数和后处理以降低表面粗糙度,本研究表明,在粉末原料中引入氧也可以降低表面粗糙度。基于XCT分析,孔隙形态和形状因素表明,孔隙主要是气孔和匙孔。气孔通常很小,具有较高的球形度(>0.8),这是由于L-PBF和粉末原料过程中Ar气流等熔池内的气体截留而产生的。匙孔是由于高能量输入而形成,孔隙较大,圆度略低于气孔。原始粉末构建的大尺寸孔隙(>40μm)是氧化粉末构建的约27倍(图7c和d)。与氧化粉末相比,原始粉末中相对较高的激光吸收(~2倍)可能使原始条件下的熔化在不稳定的匙孔过程中进行,促进匙孔诱导孔的形成(图9)。具有更高粘度的氧化熔池具有足够的润湿性,以形成均匀连续的层,且较少缺乏熔融缺陷,而参考文献中的情况并非如此。本结果表明,高氧含量的TiAl4V零件表现出比原始零件高17%的硬度。相关论文
In situ monitoring the effects of Ti6Al4V powder oxidation during laser powder bed fusion additive manufacturing
相关链接
https://doi.org/10.1016/j.ijmachtools.2023.104049
来源:增材研究,编辑:张维官,审核:王颖
声明:本文所用视频、图片、文字如涉及作品版权问题,请第一时间告知,我们将立即删除内容!